Microscopic Precision.
Custom Solutions.
Additive Screen Printing Technology taylor-made to your Specifications.
Exentis Additive Screen Printing Technology enables mass production of millions of parts with micro-precise structures like never before. These structures can be incorporated into larger components with a diameter of up to 400 mm. Furthermore, nearly every material available in powder form, such as ceramics, metals, polymers, and more, can be processed into a printable paste. You can utilize precisely the material required for your component; even porous materials are availabe.
Think big and step boldly into the future. Exentis additive manufacturing technology is your next innovation step.

Large-scale manufacturing
Production capacity of more than 5 million parts on a single manufacturing system per year.
High building rate of up to 10,000 cm3/h.

Free choice
of materials
Ceramics, metals, polymers, and nearly any material that is available in powder form.
Several materials in one component, if required.

Ultra-fine
structures
Channel width from 125 μm, wall thicknesses from 75 μm, surface quality with roughness levels 2 μm without post-processing.

Optimized
part geometries
Hollow structures to reduce weight, for parts with integrated functions, e.g. cooling structures.

Highly flexible
production technology
One production system to process all materials. Outstanding processing capability for industrial manufacturing.

Favourable
cost/benefit ratio
Lowest production costs.
No post-processing needed.

Eco-friendly
cold printing technology
Low energy consumption through cold printing technology.
High material
efficiency, only material needed for the component is processed.
The unique Exentis Technology is based on classic screen printing and expanded into the third dimension, enabling manufacturing of complex parts. Within the process the paste is pressed through a screen onto a workpiece carrier, until the parts have reached their final height. The printing process is fully automatic with a cycle time of two to eight seconds achieving a print volume of 5,000 to 10,000 cm³ per hour, depending on the details of the part. The video shows the printing process on production system EX432i for industrial applications.
Electrolyzer Plates with micro precise channels
This stainless steel electrolyzer plate is part of a membrane module used in a hydrogen fuel station. Exentis Technology allows to produce the plates in one single manufacturing step. Furthermore, the technology enables the printing of extremely fine, functional channels into the part during the manufacturing process.
Added value using Exentis Technology:
- One manufacturing step instead of several ones
- Very fine filter channels can be realized
- Manufacturing 1'050 parts in a single 24-hour shift
Engineered porosity: Optimizing membrane and filter performance
Porous materials, membranes, and multilayer systems play an important role in various applications, including filters, sensors, cooling structures, flow regulation, and more. The fact that Exentis’ additive screen printing technology uses paste feedstocks means that material composition can be exactly tailored to the requirements of a given part.
Added value using Exentis Technology:
- Manufacturing of parts that were not been possible before: porous material combined with micro-precise structural part design
Micro filter with 211 ultra-fine channels
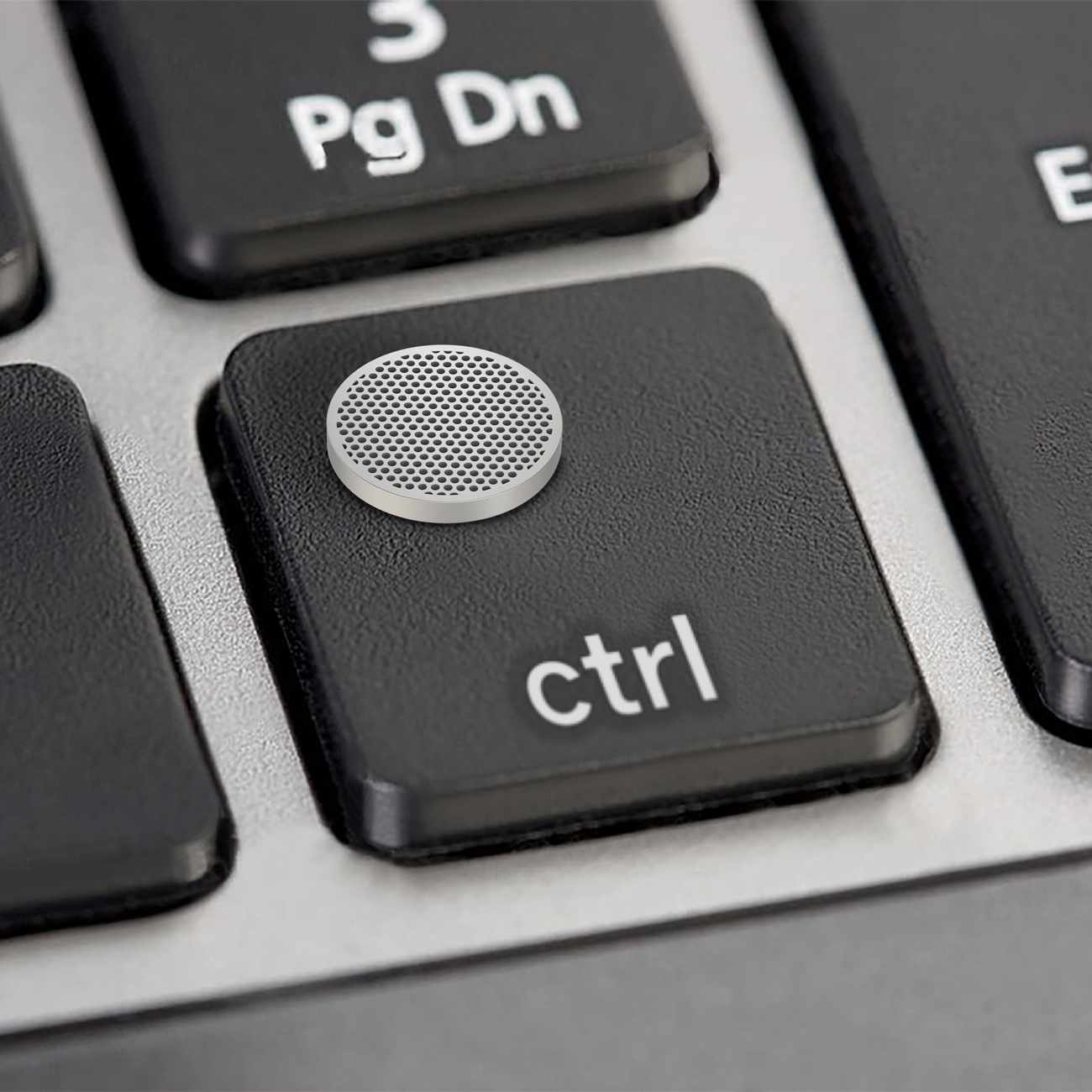
Traditionally, filters were stamped from woven mesh, which often led to quality issues due to fraying. Additive screen printing technology has significantly improved these parts, allowing for the creation of filters with very fine structures and eliminating fraying altogether. Combined with the capability for mass production in large quantities, provides an invaluable advantage for our customers.
Added value using Exentis Technology:
- Very fine structures can be realized
- No fraying: better filter properties and quality
- Manufacturing high quantities up to 5 million per year
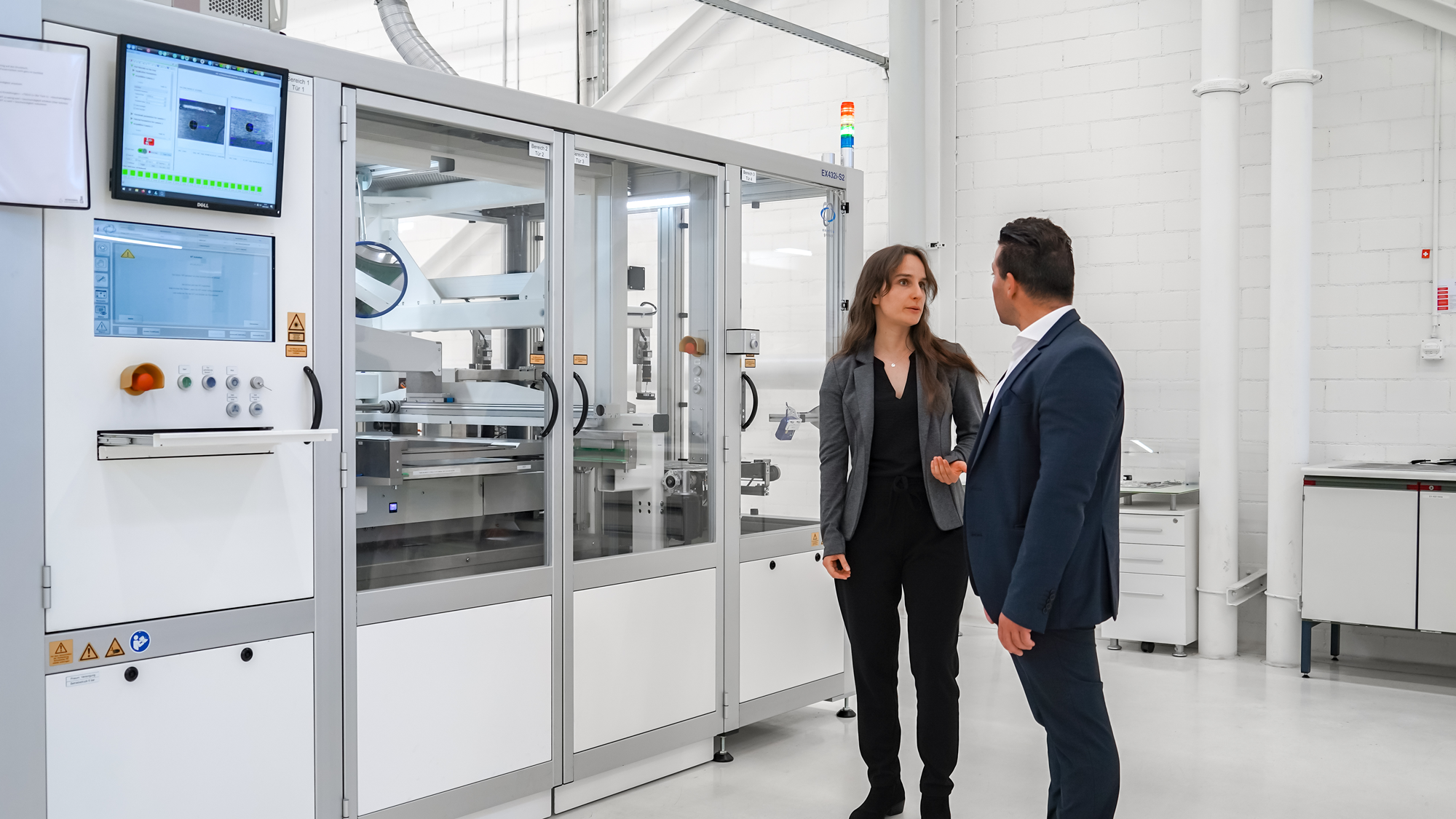
Why Additive Screen Printing should be your next innovation step
Imagine being able to produce the most complex components in quantities of millions with unprecedented precision - would you want to give it a try? In today's rapidly evolving business world, innovation is not just a buzzword - it's a necessity for the survival and growth of companies.